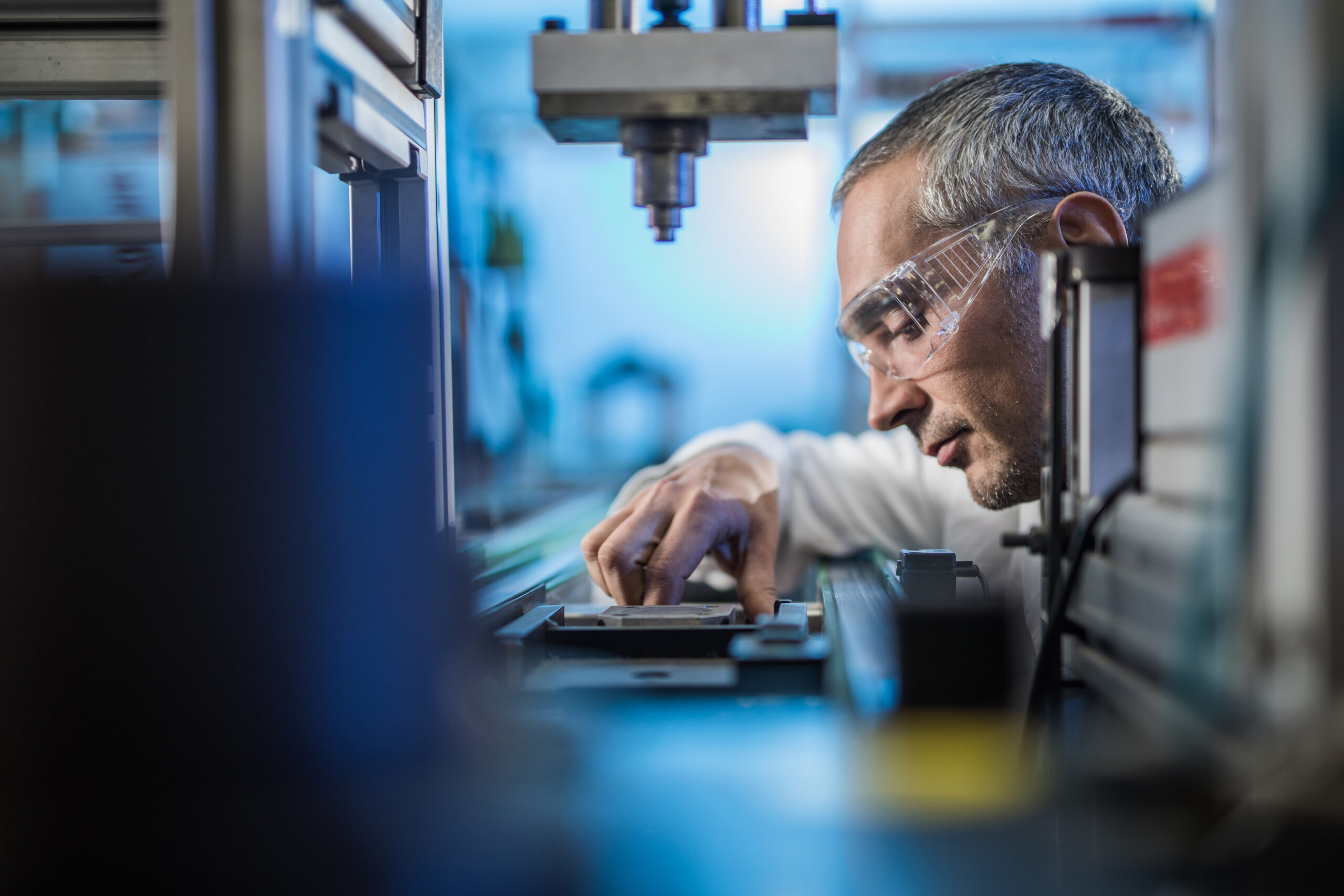
08.02.2024
Pilot testing important for cost-effective CO₂ capture
Many products in today’s market are manufactured through industrial processes. That release substantial amounts of CO2. Hence it is imperative for the industry to find cost-effective solutions to avoid CO2 being released into the atmosphere.
Pilot plants serve as small-scale process facilities where technology providers and industry can collaboratively test and demonstrate CO2 capture technologies. This occurs under realistic conditions, often preceding decisions on full-scale implementation.
Avoiding costly mistakes
– A pilot plant provides the opportunity to refine the technology. Challenges can be identified and addressed on a smaller scale.Minimizing the risk of expensive errors during implementing. And operation in full-scale facilities. It also allows for improvements and innovations enhancing the technology’s long-term cost-effectiveness, says Svein Bekken, Senior Adviser at Gassnova.
A pilot plant also provides valuable knowledge through learning. Benefitting both technology providers and technology users (the industry). Understanding how the technology reacts under real conditions. Considering emissions, temperatures, and other operational factors. Enables providers and customers to evaluate and optimise the capture system’s performance. Ensuring its robustness for full-scale implementation in any industrial scenario.
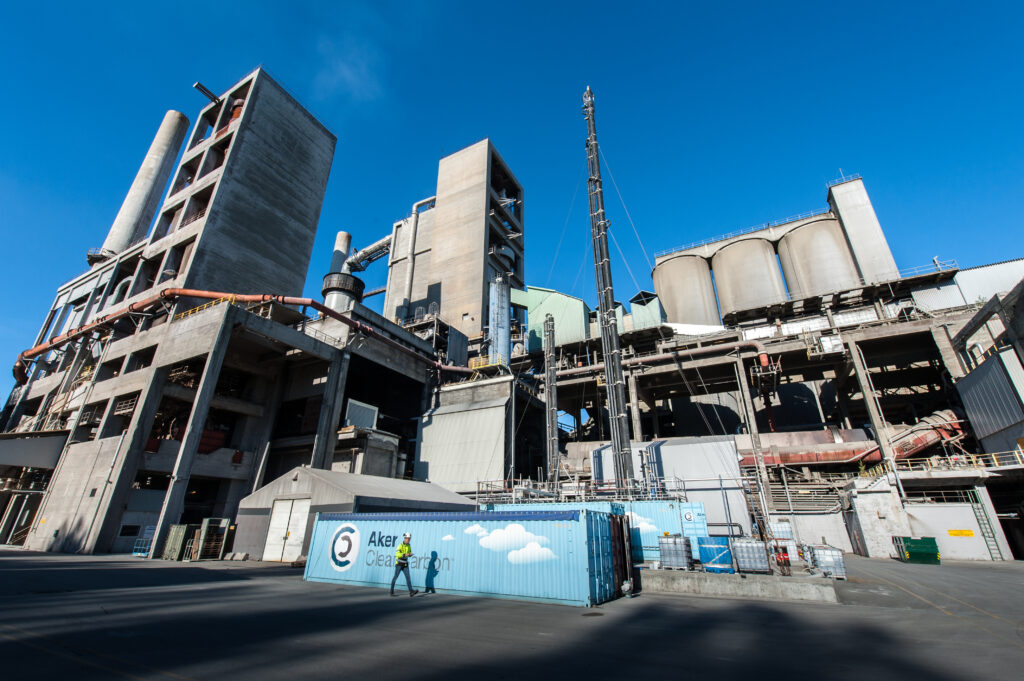
Cost-efficient and sustainable technology
To achieve climate change targets. CO2 capture technology is a key component for much of the energy intensive industries. Both nationally and internationally. Testing their technology under real industrial conditions is essential for providers. As it is impossible to simulate or predict all the challenges in an industrial context.
– At the same time. It is crucial for industrial companies (CO2 emitters) to gain knowledge about the capture technology they might implement in their own plants. This includes knowledge of what is required in terms of preparation. And changes to the infrastructure in and around their own facilities, says Jørild Svalestuen, Senior Adviser at Gassnova.
The Lesson Learned report from Longship shows that 34 percent of the costs of CO2 capture are related to infrastructure (“Utility and Support Systems”). Early phase of pilot testing is very useful for both technology providers and technology users (CO2 emitters), especially for industries where CO2 capture has not been tested previously.
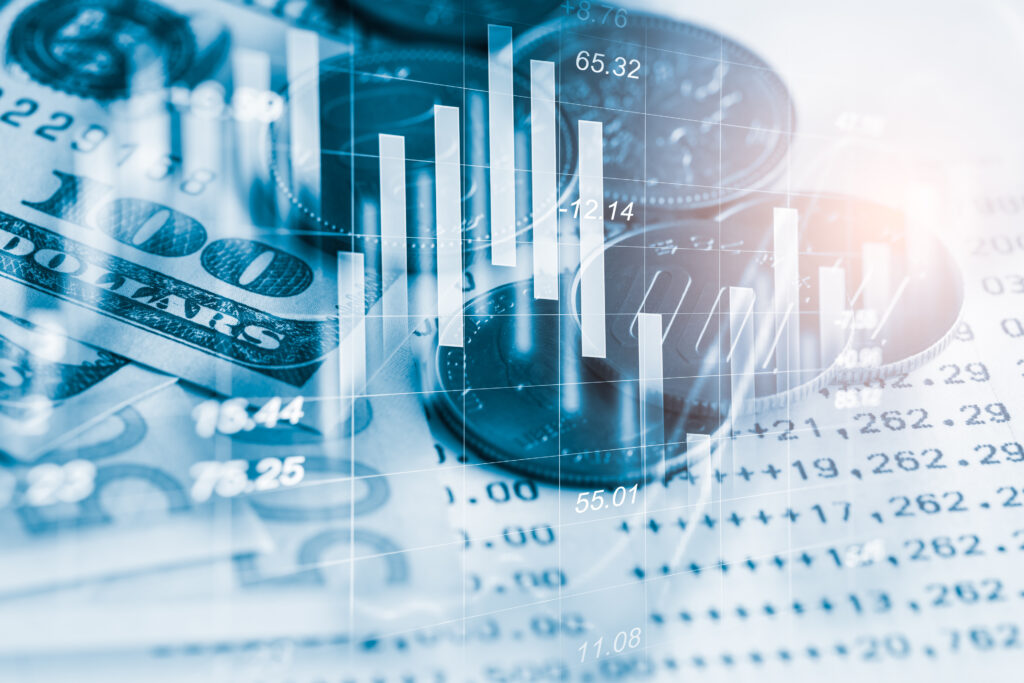
Interaction with the industry
CLIMIT has supported pilot tests at facilities such as: SINTEF’s CO2 capture pilot test centre at Tiller, Trondheim, the Technology Centre Mongstad (TCM) and mobile test units owned by various technology providers. Below are examples of companies that have tested their technology with support from industry and CLIMIT:
- Aker Carbon Capture has at the request from industry, demonstrated its own capture technology in different type of industries using a mobile test unit. These include companies such as Heidelberg Materials in Brevik, Hafslund Oslo Celsio in Oslo, Preem AB in Sweden, Polchar in Poland, Elkem and SMA Mineral in Mo Industripark. In earlier phases, the solvent technology was tested and optimised in collaboration with NTNU and SINTEF. The technology was further tested, developed, and qualified at TCM for further use at larger scale.
- Hydrogen Mem-Tech’s technology for separating hydrogen from CO2 has been tested under real conditions at Equinor’s plant in Tjeldbergodden.
- Baker Hughes’ Compact Carbon Capture technology, developed in Norway in collaboration between Fjell Technology Group, Equinor and SINTEF – with support from CLIMIT. The technology has been tested at Equinor’s pilot plant in Porsgrunn.
- Fjell Technology Group’s Moving Bed Carbonate Looping technology, developed in collaboration with NTNU and SINTEF, is scheduled for pilot testing – with a mobile unit under construction for testing in industrial environment.
- Air Products in Kristiansand has tested two types of membranes for CO2 capture at Heidelberg Materials in Brevik. They are currently being testing their commercial membrane at Returkraft in Kristiansand.
- SINTEF’s patented CSAR (Continuous Swing Absorption Reactor) CO2 capture technology will be tested at Bergen Area Inter-Municipal Waste Disposal Company (BIR).
The CLIMIT programme has been making a difference for almost 20 years. Supporting the development of CO2 capture technologies and conducting pilot-scale testing in industrial conditions. Has been significant for technology providers and the industry that will adopt this technology.